
Safety
At Croda we believe safety is a value, at the forefront of this approach to safety and values-driven cultural change are our leaders, who consistently and authentically show that we care about our employees in everything they do. All senior leaders within Croda have committed to this, with personal development plans monitored by the Group CEO.
The safety of our employees and neighbours is, and always will be, of paramount importance. Through our focus on safety, we will directly contribute to the following UN SDG targets:
SDG 3.4, SDG 3.9
Good health and well-being
SDG 8.8
Decent work and economic growth
Meaningful safety conversation to drive focus
Our new Human Performance Programme, developed in 2021, has been rolled out to six pilot sites. This creates opportunities for meaningful conversations about how work is carried out, exploring the risks that people face, and to empower all employees to get involved and provide solutions. In the first six months of the trial, more than 100 improvements were identified across only the six sites involved. Resources are being allocated to enable a full rollout in the next two years. This is now active across all regions and lead to more than 2500 improvements in 2024.
In 2024, we conducted a Safety Culture Survey for manufacturing and warehousing operations at more than 40 global locations, with a high engagement level of 85%. Whole-organisation pulse surveys have also included questions on how we work together in a safe way. The results have allowed us to identify locations that require focus, informing local, regional and senior leadership reviews as we continue building a picture of what is required to keep everyone safe when they work at Croda.
Process safety
For companies that store, use and produce hazardous materials, safe and effective management is critical. Our process safety management system is based on standards and guidance from the UK Health and Safety Executive together with best practices from regulators and industry bodies worldwide. As part of our process safety management system, all process risk reviews on manufacturing sites are subject to regular periodic reassessment by a team that includes specialists from our Safety, Health and Environment function and external experts.
We also contribute to and in some cases hold leadership responsibility for several industry associations and best practice groups, including Responsible Care® initiatives aligned with national chemical industries associations.
Extending our measuring and reporting to cover all likely incidents, going beyond the standard approaches, we established the performance measure of Process Safety Incident Rate that records all types of incidents, such as demands on relief streams and plant control systems, rather than purely losses of containment. This internal measure was created as other external benchmarking conventions focused on losses of containment and did not take the holistic view of process safety we felt was needed. However, to enable global benchmarking with other organisations, we will also measure incidents using established external indexes from the International Council of Chemical Associations (ICCA) and Sustainability Accounting Standards Board (SASB).
Case study: Safety as a value
Small improvements make a big difference to safety in Thane, India
At our Thane site, cross-functional human performance teams have identified 688 improvements in just 12 months that will enhance personal and process safety as well as more efficient operations. One process improved through this approach is the handling of a hazardous raw material. The material is received in large plastic containers that need immediate cleaning out once emptied. The task was time-consuming, uncomfortable and physically demanding. Recognising these risks, our human performance team discussed and developed a low-cost, effective mechanism to make the work environment safer, that required minimal investment. This decontamination station was trialled in one plant, where the operators noted significant improvements in workplace safety. The concept was then installed site-wide. “Previously, contaminated containers were cleaned individually in a difficult location,” said Anil Jadhav, an experienced operator. “Now, we have installed a self-contained water flushing system for multiple containers, and configured it to make it easier to use with lower safety risks. This change also helps reduce the time required to clean each container.”Human Performance programme: a global initiative to embed safety as a value
The improvements at Thane are part of our broader Human Performance (HP) programme, which aims to enhance safety, health, and environmental (SHE) leadership across Croda. The programme focuses on understanding people, promoting empathetic engagement, and developing trust. Since its inception in February 2022 with pilot training courses at our Rawcliffe Bridge site in the UK, the programme has gained momentum, with training delivered across all regions and all leadership levels within the Group. More than 60 champions have been recognised. These champions are tasked with training leaders within their part of the organisation, encouraging and coaching them to drive improvement. By the end of 2024, champions training has been completed in all four regions, ensuring that every operating site across Croda has at least one trained champion. This rapid development and deployment of champions has strengthened the programme, fostering meaningful engagement through the cross-functional, local learning teams approach to drive improvements in our work practices. Our Human Performance programme continues to evolve, driving positive change and reinforcing our commitment to safety and operational excellence across the organisation.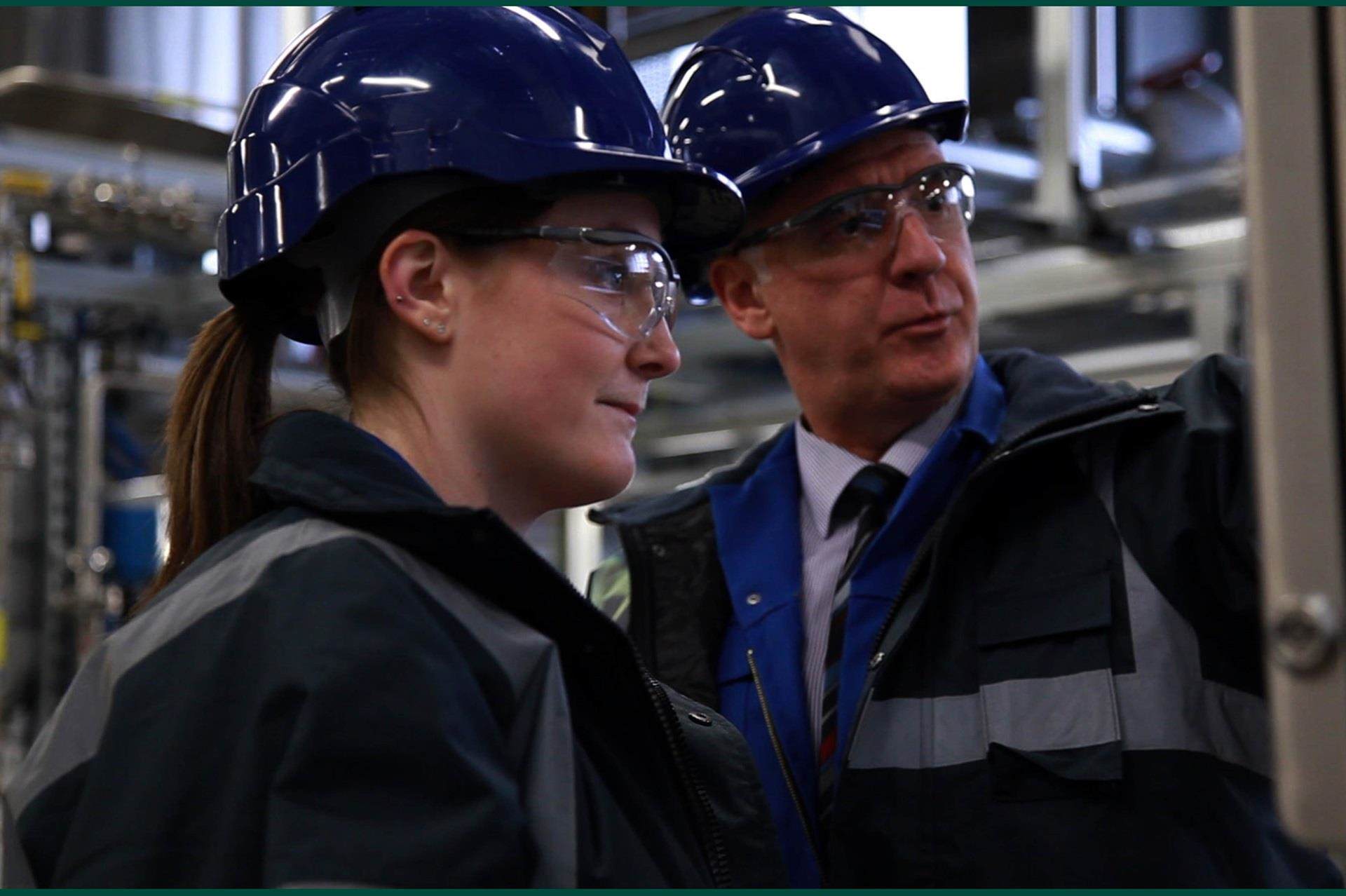